By Nick Christians, Ph.D., Ben Pease, and Adam Thoms, Ph.D.
Tank mixing of fertilizers and pesticides can be a very efficient method of applying these materials to your turfgrass, but it must be done carefully. Small mistakes, such as putting a decimal point in the wrong place, can be costly, and can even kill the turfgrass. The order in which the various chemicals are added to the tank is also important, and minor mistakes can result in major problems in the tank with chemical and physical incompatibility.
When it comes to tank mixing, mathematics is critical. For a more detailed description of the math involved in tank mixing, see “The Mathematics of Turfgrass Maintenance” (Christians and Agnew, 2008). The following are some of the basics from that book.
The first consideration has to do with the type of sprayer that is being calibrated. If you are blessed with one of the new GPS (Global Positioning System) sprayers, you can simply set the number of gallons per acre in the computer system. However, you should never completely trust a computer. It is always critical that you back this up by performing the procedures outlined here, at least initially, and periodically check the application rate of the system on a known area of turfgrass.
Most of us are not going to be able to spend $50,000 or more on the latest equipment. That means that we likely have a standard sprayer with a tank, boom and multiple nozzles that rely on us to calibrate the system. At first, this is going to appear to be very complex, but actually the process is not difficult once you understand the basic logic involved. There are basically two steps involved:
1. Determine how long that it takes your sprayer to cover an acre of turfgrass.
2. Determine how much liquid is released in that amount of time.
Before we start, we have to establish some facts. There are many things that affect application rate, including pounds per square inch (psi) of pressure generated by the pump, the number of revolutions per minute (rpm) of the engine, gear and gear range of operation, and the speed of the unit. Speed is critical. If the flow rate remains constant and speed drops in half, you will be applying twice the desired rate of application. These things can vary, so, from the beginning, establish these criteria and stick with them throughout the calibration and application process.
Other key pieces of information include the size of the tank on your unit, the width of the boom, and the number of nozzles on the boom. Write all of this information down as you gather it, and then you are ready to begin.
Next we have to determine the operating speed at which the applications will be made. Don’t even look at the speedometer, as it can be highly inaccurate and will be of little use in this process. We are going to do a little experiment to determine the operating speed. First, determine your gear and gear range for application. Next, set the operating speed at a constant number of engine rpm. Then get a stopwatch and set up a known distance on which to operate the unit. In this example, we are going to place flags at a 100-foot distance and we are going to be working with a unit that has a 15-foot-wide boom. Now, have the person who is going to be doing the actual applications drive the unit at a uniform speed over the 100-foot distance. Have a second person use the stopwatch to accurately time this process. It is a good idea to do this three or four times and determine a mean time to travel 100 feet.
In our example, we find that it takes an average of 14 seconds to travel the 100 feet (this will vary from sprayer to sprayer). We have now established a very important fact. The sprayer boom is 15 feet wide and the time required to cover the distance is 14 seconds. Therefore, 15 ft. x 100 ft. = 1,500 square feet. It takes 14 seconds for the sprayer to cover an area of 1,500 square feet.
Next, we need to know how long it will take this sprayer to treat an acre of turfgrass. We do this by setting up a simple proportion, followed by cross-multiplying and dividing to get our answer.
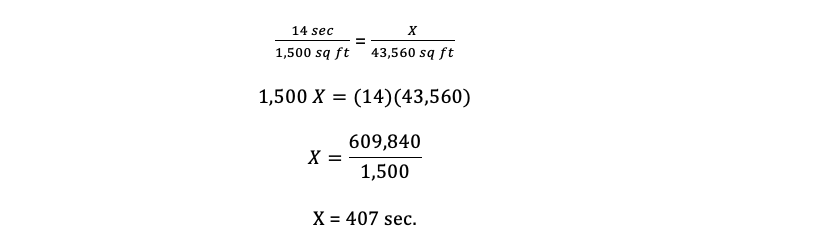
We have now determined that it will take 407 seconds to cover an acre (43,560 square feet). Write this down, as it is the critical first step.
The next step means going back to the facts that we have established. In this example, we have a 100-gallon tank; we are operating at 30 psi, with an engine speed of 1,500 rpm. The 15-foot boom has 10 nozzles.
Next, we need to collect a little data. To do this, we will need some measuring cups large enough to catch the spray volume from a few seconds of operation. You will need to set up the proper operating conditions. Start the sprayer, set it to the right number of engine rpm, and catch the spray from each nozzle. The amount of time that you do this can vary. In this example, we are going to use the same time that it took to travel 100 feet, which is 14 seconds. It is a good idea to check the flow rate of every nozzle to determine if any nozzles need to be replaced due to wear. A nozzle with a difference as small as 10% should be replaced. This can greatly affect flow rate from the individual nozzles.
In our current example, we have determined that an average of 17.5 ounces (oz.) is released from each nozzle in 14 seconds. There are 10 nozzles, therefore
17.5 oz. x 10 nozzles = 175 oz. A total of 175 oz. of liquid is released from the sprayer in 14 seconds. We can now easily determine the application rate of the unit.
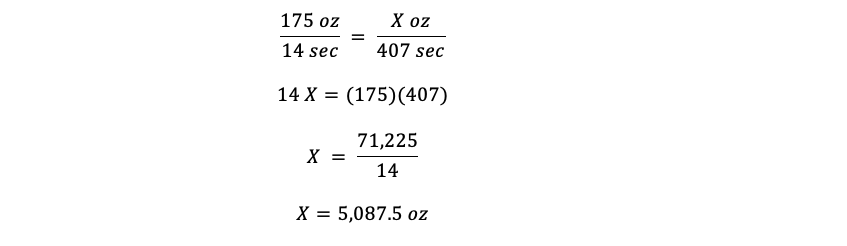
There are 128 oz./gal; therefore:

We now know that this sprayer, at these operating criteria and speed, will apply approximately 40 gallons of spray per acre to the turfgrass. We also know that we have 100 gallons in the tank, therefore we can cover
100 gallons/40 gallons per acre = 2.5 acres per tank
43,560 square ft./acre x 2.5 acres = 108,900 sq. ft.
The fact that we will treat 2.5 acres or 108,900 sq. ft. with a tank is important information for the next step.
Next, we will calculate how much fertilizer and how much pesticide will be placed in the tank for the spray application. In this example, we will tank mix a liquid fertilizer (14-0-3) with 1.4 pounds (lbs.) nitrogen (N) per gallon of product at a rate of 0.5 lbs. N/1,000 sq. ft., a 4 emulsifiable concentrate (EC) herbicide at 2 quarts (qts.) per acre, and a 50 wettable powder (WP) insecticide at 1.5 lbs. a.i. (active ingredient)/acre.
Let’s begin with the fertilizer. When dealing with liquid fertilizer, it is not the analysis that is important; it is the number of lbs. N/gallon. In this case, it is 1.4 lbs. N/gallon. We know that the material contains 1.4 lbs. in one gallon and we only want 0.5 lbs. N for each 1,000 sq. ft., therefore the answer will be less that a gallon per 1,000 sq. ft.
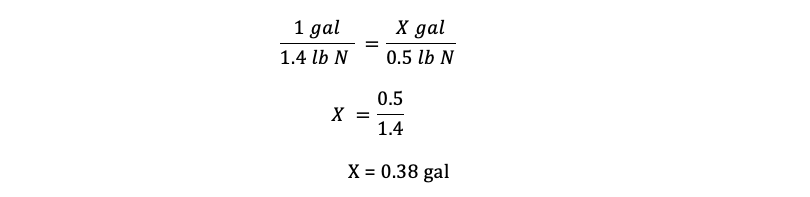
We now know that we need 0.38 gallons of 14-0-3 fertilizer for every 1,000 sq. ft. of area treated. The tank will treat 108,900 sq. ft., therefore:
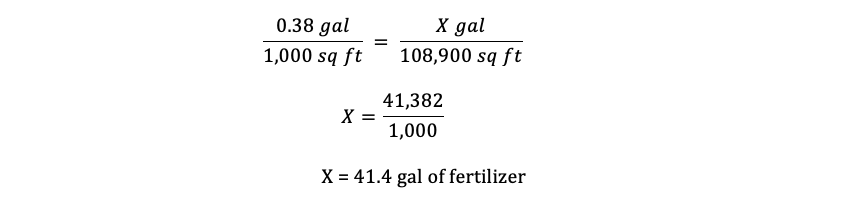
Therefore, when we prepare a tank of material, there needs to be 41.4 gallons of fertilizer added to each tank load.
Next, determine how much 4 EC herbicide goes in the tank. We know the application rate is 2 qts./acre, therefore:
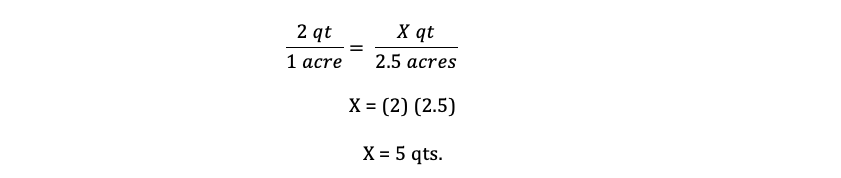
We will need 5 qts. of the herbicide in each 100-gallon tank.
Finally, the insecticide is a 50 WP to be applied at 1.5 lbs. a.i./acre. We can calculate the amount of product per acre in this way:

We now know that we will need 7.5 lbs. of 50 WP insecticide per tank.
In summary, we know that we need 41.4 gal. of 14-0-3 fertilizer, 5 qts. of 4 EC herbicide, and 7.5 lbs. 50 WP insecticide in each tank of material. We will then bring it to 100 gallons volume with water and mix it thoroughly. We are then ready for the spray application. Each acre will be treated with 40 gallons of total spray volume. Each 1,000 sq. ft. will receive 0.5 lbs. N. The herbicide will be applied at 2 qts./acre (2 lbs. a.i./acre), and the insecticide will be applied at 1.5 lbs. a.i./acre.
There is one more consideration that we will need to deal with before we start mixing. That is the order of adding the materials to the tank. This can be very important, particularly with a variety of formulation like we have in this example. In the next article, entitled “Tank Mixing Procedures,” Ben Pease will consider the order in which various formulations are to be added to the tank, and some of the other practical aspects of tank mixing.
Nick Christians, Ph.D., is a university professor of horticulture at Iowa State University. His specialization is turfgrass science. He is the author of more than 1,200 articles and research papers related to turfgrass management.
Ben Pease is a Ph.D. candidate and turfgrass research scientist at Iowa State University. He received his undergradate and graduate degrees from the University of Wisconsin-Madison. Prior to returning to school, Pease spent six years as an assistant golf course superintendent. His research has focused on bentgrass shade tolerance, Kentucky bluegrass traffic tolerance, and compost use during establishment.
Adam Thoms, Ph.D., is assistant professor specializing in commercial turfgrass management, Iowa State University, Department of Horticulture, Ames, Iowa.
Literature cited
Christians, N.E. and M.L. Agnew. 2008. The Mathematics of Turfgrass Maintenance. John Wiley and Sons. ISBN 978-0-470-04845-0. 160 pages